WIRTGEN milling and cutting drums
WIRTGEN can also provide customised solutions which are suitably matched to the operating conditions concerned if special milling techniques should be required in specific cases.
WIRTGEN milling drums for cold milling machines
Maximum versatility
The milling drum must fulfil three main tasks:
- Cutting and breaking out of material particles from the compound.
- Conveying: Transport of the separated material particles to the area of the ejector.
- Ejection of the removed material particles onto the loading conveyor.
To make optimum use of the machine’s potential, WIRTGEN offer a variety of different milling drum types which differ in their tool spacing and the maximum possible milling depth, which are determined by the application.
Examples of different types of milling drums for small milling machines
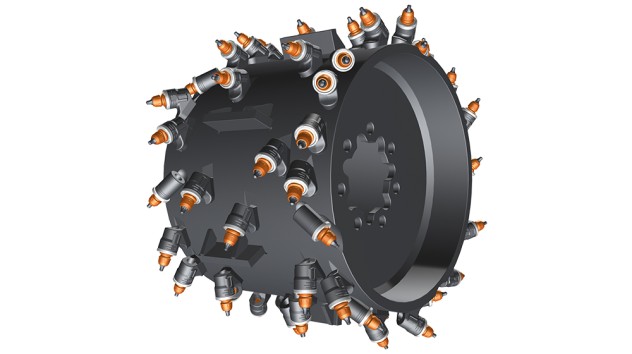 |
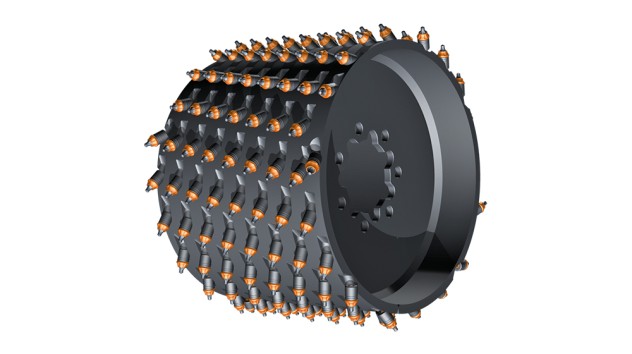 |
Milling drum LA15: milling drum with 15 mm tool spacing. |
Micro-fine milling drum LA3: milling drum with 3 mm tool spacing for fine milling |
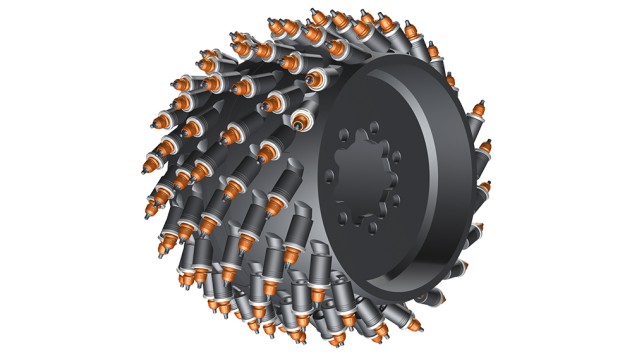 |
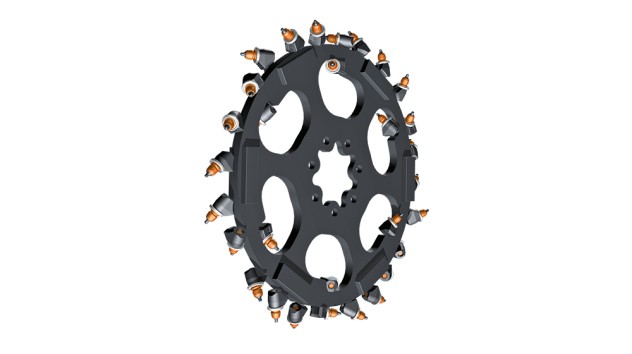 |
Water channel milling drum LA4 FB500: milling drum with 4 mm tool spacing and a milling width of 500 mm for creating water gutters |
Cutting wheel: specially designed milling drum for trenching applications |
Examples of different types of milling drums for compact and large milling machines
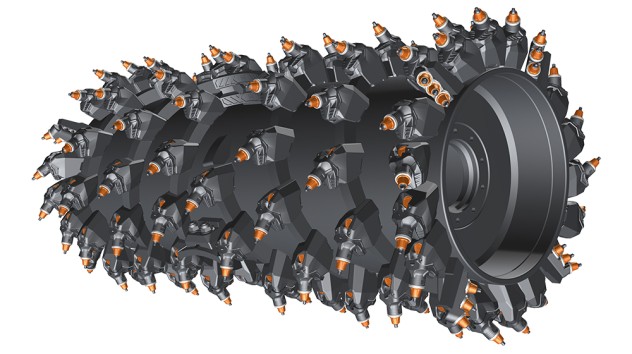 |
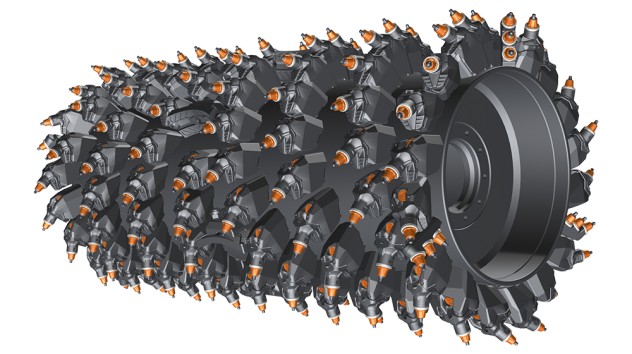 |
ECO Cutter: for greater demands on volume performance (e.g. complete road removal, concrete milling work)
Milling depth: up to max. 350 mm, tool spacing: 20 - 25 mm |
Standard milling drum: universal milling drum vor versatile use (e.g. removal of surface or binder course)
Milling depth: up to max. 350 mm, tool spacing: 12 - 18 mm
|
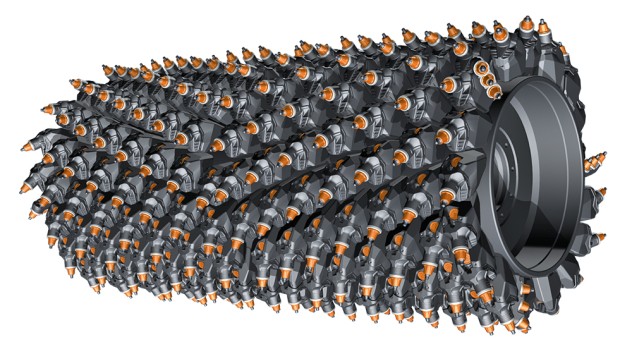 |
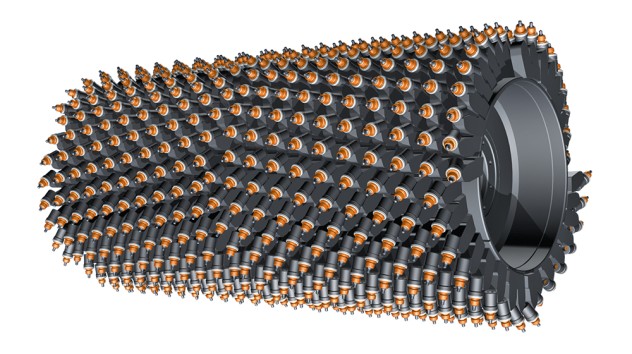 |
Fine milling drum: for high demands on profile (e.g. removal of surface courses, corrective milling work on road profiles)
Milling width: up to max. 80 mm, tool spacing: 8 - 10 mm
|
Micro-fine milling drum: For the highest demands on profile (e.g. increase in surface grip by roughening road surfaces, Preparation milling for surface treatment and cold paving of this layers, Removal of road markings)
Milling width: up to max. 30 mm, tool spacing: 3 - 6 mm |
Quick exchange of milling drums using FCS
The optional Flexible Cutter System, abbreviated as FCS, allows operators to change milling drums quickly and easily to use different working widths, line spacings or milling profiles. Highly versatile, the FCS opens up a whole variety of cold milling machine usage options to ensure maximum cost-effectiveness.
- FCS - Exchanging milling drums of different widths, with different tool spacings and milling profiles (example: small milling machines)
- FCS Light - Exchanging milling drums of identical width but with different tool spacings and milling profiles (example: large milling machines)
WIRTGEN milling and mixing rotors for cold recyclers and soil stabilizers
DURAFORCE - A single rotor catering to all requirements
Challenging operating conditions such as the powerful cold recycling, granulation or stabilization of coarse-grained soils make ex-treme demands on the cutting tools. This calls for perfectly matched components designed to meet the highest performance requirements. They can be relied on to provide high milling and mixing performance while ensuring maximum resistance and durability at the same time.
The original WIRTGEN DURAFORCE milling and mixing rotor impresses with extreme wear resistance, impact strength and frac-ture strength for all applications in soil stabilization and cold recycling: a single rotor catering to all requirements."
Outstanding features of the DURAFORCE milling and mixing rotor
High-performance soil stabilization
Soil stabilization, which is in use around the globe, represents the ideal solution for converting subsoils of insufficient bearing capacity into soils suitable for placing and compacting. In the process, a wide variety of different types of soils need to be processed which may be highly cohesive, abrasive or even interspersed with coarse-grained rock.
Requirements on the milling and mixing rotor:
- Effective splitting and crushing of the soil to optimize binder effectiveness
- Uniform distribution and homogeneous mixing of binders and, where appropriate, water to produce a mixture of high strength
- Maximum cutting performance even in tough, hard soil to ensure high productivity and low fuel consumption
- High fracture strength when operating in soils interspersed with coarse-grained rock to ensure extended uptimes
- High wear resistance in abrasive, cohesive soils to ensure maximum economic efficiency
Environmentally friendly cold recycling
Cold recycling and granulation are also internationally established construction processes. Distressed asphalt pavements comprising the most diverse types of rock and the underlying gravel layer are milled, usually mixed with added binders to produce a homogeneous material and then placed again in an in-situ process.
Requirements on the milling and mixing rotor:
- Steady milling process to prevent oversized particles and to ensure high-quality results
- High milling performance and low wear even in hard, abrasive material to ensure high economic efficiency
- Compliance with the specified grading curve to ensure the permanent structural integrity of the new base layer
- Homogeneous mixing of the binders to ensure high adhesion (bonding strength) between the individual particles and thus maximum bearing capacity
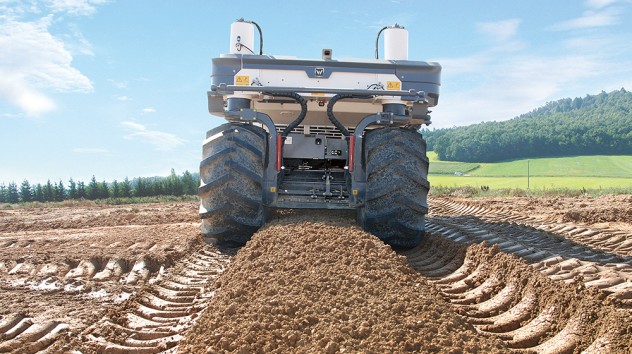 |
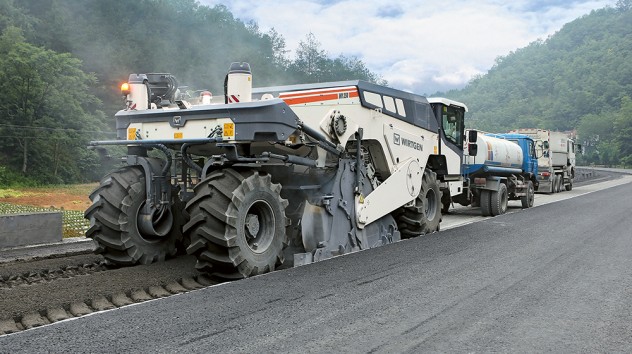 |
The tried-and-tested WIRTGEN DURAFORCE milling and mixing rotor meets every challenge in soil stabilization and is the ideal candidate to convert even the most difficult soils into construction materials of superior quality. |
The DURAFORCE milling and mixing rotor also handles the specific requirements of cold recycling. Users benefit from maximum performance, an extended service life and highest quality of the new base layers. |
Unrivalled expertise from a single source
WIRTGEN offers high-performance cutting systems from a single source. From a single source means perfectly matched components and consistently impeccable quality. The DURAFORCE milling and mixing rotors combine expertise gained in many decades with mature manufacturing methods and forward-thinking technologies.
Field experience and customer feedback are important factors feeding directly into the process.
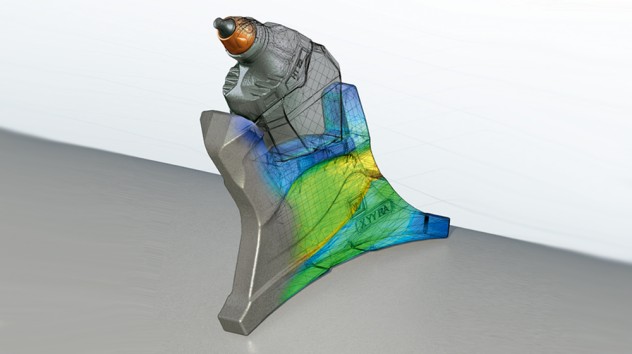 |
Solution-driven engineering
State-of-the-art work equipment – such as professional simulation tools – is an essential ingredient of WIRTGEN’s standard tools of the trade. It forms an integral part of the highly complex engineering process to determine the ideal solution. A prime example of this is the holder base. In combination with the selected alloy, its defined geometry results in high wear resistance, the best possible weldability and even load distribution, thus offering reliable protection against excessive loading of the holder base. High shear forces, in particular, are deflected most efficiently in this way.
|
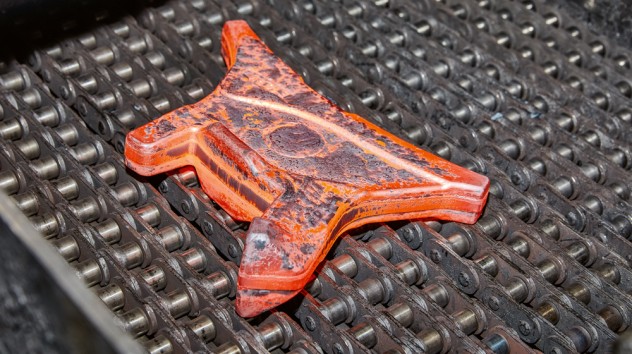 |
Tried-and-tested forging process
The holder bases of the DURAFORCE milling and mixing rotor are given an intelligently designed 3D geometry using the tried-and-tested forging process. In addition to even load distribution and thus maximum stability, this process results in an optimum flow of material and homogeneous construction material mixtures.
|
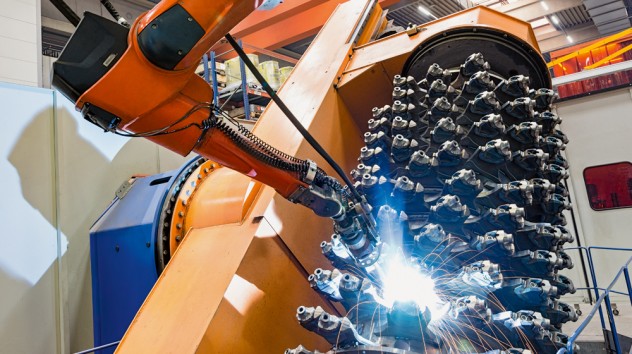 |
Automated welding processes
Final welding of the quick-change toolholders and holder bases on the DURAFORCE milling and mixing rotor is effected using welding robots. Our welding robots provide a maximum degree of process reliability, precision and quality of the welding seams, guaranteeing fast and efficient production processes.
|
 |
Precise balancing
The milling and mixing rotors, which can weigh up to 4,500 kg, operate at significantly higher milling speeds than the milling drums installed in cold milling machines. That is why each single rotor produced at the WIRTGEN plant is balanced with meticulous care. The resulting perfect concentricity of the rotor not only considerably extends the useful life of the entire machine but also protects the machine operator from vibration.
|
WIRTGEN cutting drums for Surface Miners
Configuration tailored to requirements
For each application, we are making every effort to optimize the cutting performance while at the same time maximizing the service life and minimizing operating costs. To achieve this goal, the cutting drum and toolholder system are given a heavy-duty design tailored to performance requirements in accordance with the type of rock to be mined, rock hardness and material gradation.
Depending on the material to be mined, different drum and pick configurations are available for each type of machine. Based on the material properties and rock hardness, the optimum solution in terms of the drum diameter with picks, pick spacing, holder bases and additional special equipment for increased wear resistance is determined in close cooperation between the customer and WIRTGEN experts.
Công nghệ khác
WIRTGEN toolholder systems
WIRTGEN picks and cutting tools