WITOS FleetView - And everything runs smoothly
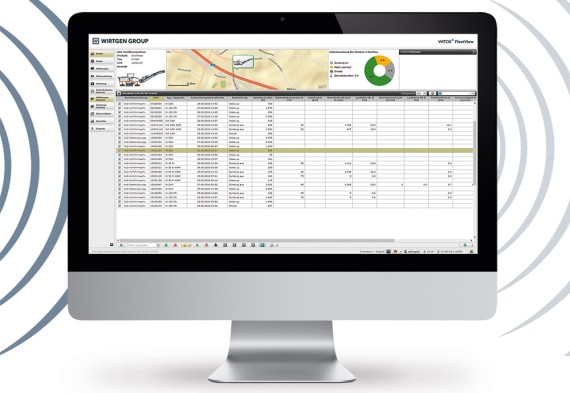
WITOS FleetView gets the machines of WIRTGEN, VÖGELE and HAMM communicating: every unforeseen fault, along with every due inspection, is displayed on the WITOS FleetView web application.
A penny saved is a penny earned. WITOS FleetView is a must-have for anyone who takes this old proverb to heart. That’s because the telematics solution from the WIRTGEN GROUP offers users and machine operators a wide range of advantages that translate into hard cash. A real-life example confirms: GSI-Asphalt, a medium-sized enterprise, have been relying on WITOS FleetView in conjunction with the Smart Service agreement for many years now. Both services guarantee maximum machine availability – enhancing the cost-efficiency and value retention of the machinery.
A powerful medium-sized enterprise specializing in fibre-optic expansion
GSI-Asphalt is a successful SME that has been growing steadily for years. There are good reasons for this: efficient processes, a high quality standard and a business model that is geared to the local authority sector, particularly the construction of utility lines and the expansion of the fibre-optic network. The modern machine fleet of the WIRTGEN GROUP – and the WITOS FleetView and Smart Service packages – make a key contribution to the company’s efficiency and quality. Indeed, these two strategic instruments enable GSI-Asphalt to get more out of their investment: “The due inspections and service intervals are scheduled by the WIRTGEN GROUP for all the machines,” explains Werner Aicher, Managing Director of GSI-Asphalt, highlighting a key advantage of WITOS FleetView. The telematics solution enables the WIRTGEN GROUP to analyse service-related parameters such as operating hours and send notifications of upcoming inspection services. It goes without saying that the data are also available to the customer and the customer’s staff too, where appropriate.
Perfect interplay between the customer GSI-Asphalt and the WIRTGEN GROUP: the machine fleet automatically transmits service-related data to the customer and the WIRTGEN GROUP sales and service company via the WITOS FleetView telematics solution. The subsidiary in Augsburg then schedules the service appointments in consultation with GSI-Asphalt.
WITOS FleetView slashes downtimes
“The telematics solution is straightforward, and we don’t have to keep thinking about our machines,” says Aicher. “The system has significantly increased the capacity utilization of our machine park. What’s more, we can always be confident that there will be no avoidable trips to the workshop during a construction project. As a result, our operations can be planned more effectively and are more cost-efficient, too, because we always have three weeks’ notice ahead of service appointments, enabling us to reschedule machines if necessary or make use of substitute WIRTGEN GROUP machines. So there’s no disruption to the work.” And once a machine is due for servicing, the Smart Service helps contractor GSI-Asphalt keep costs down. Anyone using a variety of machines from WIRTGEN, VÖGELE and HAMM or – as in the case of GSI-Asphalt – with a fleet made up entirely of WIRTGEN GROUP products, enjoys further benefits: the central contact at the relevant WIRTGEN GROUP subsidiary can coordinate a single service or maintenance appointment for multiple WIRTGEN, VÖGELE and HAMM machines. This further increases machine availability.
WITOS FleetView at a glance
WITOS stands for “WIRTGEN GROUP Telematics and On-site Solutions” and is the name given to the software product family of the WIRTGEN GROUP that supports customers, operators and users above and beyond the machine hardware.
WITOS FleetView makes fleet and service management for WIRTGEN, VÖGELE and HAMM machines even more efficient, because the system-based visualization and analysis of machine and position data give machine managers and users an overview of their machine fleet at all times. While the Smart Service agreement provides for regular inspections in accordance with the instruction manual, WITOS FleetView additionally supports proactive maintenance planning and a rapid response in the event of faults.
How WITOS FleetView works
The telematics control unit (TCU) installed in the machines collects, compresses and stores the machine data. The data are then sent in encrypted form via GSM to the WIRTGEN GROUP data centre, where they are analysed and made available to the customer
WITOS FleetView – The functions in detail
WITOS FleetView supplies the data in a user-friendly web application with clear and well organized submenus. An overview of the most important functions:
Fleet:
This menu provides a compact overview of the current operating status of a company’s machine fleet. One or several machines can be selected for more detailed views and analyses.
Map
The map view shows the current location of one or several machines. The machine path function enables you to track the route that the machine takes during operation and transport.
Monitoring
With these functions, it is possible to define times when and places where the machines of a fleet are permitted to operate. If monitoring protection is activated, operators are given immediate notification by e-mail in the event of unauthorized access to the machine. Notifications can be defined for alarms and faults as well as maintenance dates.
Operation data / History
The history view allows operational and position data to be displayed for the machines over a freely definable period, in a clear and easily readable layout. These data can also be exported.
Messages / History
All current and past messages from the machines at a glance: the history view can be used to generate an individually defined summary. All messages are displayed and described just as they appear on the machines. The clear message categorization and the documentation provide information on the service status of the machines.
Maintenance / History
The history view of the maintenance section contains all the information required to ensure optimally maintained machinery. Be it information on the type and scheduling of upcoming maintenance work or maintenance reports on previous workshop visits, the maintenance functions reliably ensure that the entire machine fleet remains operational.
Reports
Eight predefined reports on the machine capacity utilizations and the fleet overview are available to the user. These can be displayed as daily, weekly, monthly or annual overviews and can also be exported.
One-stop service
With WITOS FleetView, servicing has become a more automatic process for GSI-Asphalt – but without losing the personal touch. Thomas Weber of the WIRTGEN GROUP subsidiary in Augsburg has for years been a dedicated point of contact for GSI-Asphalt, attending to all concerns – which of course extend beyond the service information provided by WITOS FleetView. “We genuinely profit from the rapid response times, even when we have questions or want to make use of the application-specific advice. This bolsters our view of the WIRTGEN GROUP as a true partner whose loyal support can be relied on,” says Werner Aicher.
Công nghệ khác
VÖGELE Get the Job Done Accurate to the Millimetre
“AutoSet Plus” is Quality Assurance at the Press of a Button
SprayJet versus Conventional Paving with Pre-Spraying of Emulsion